
01
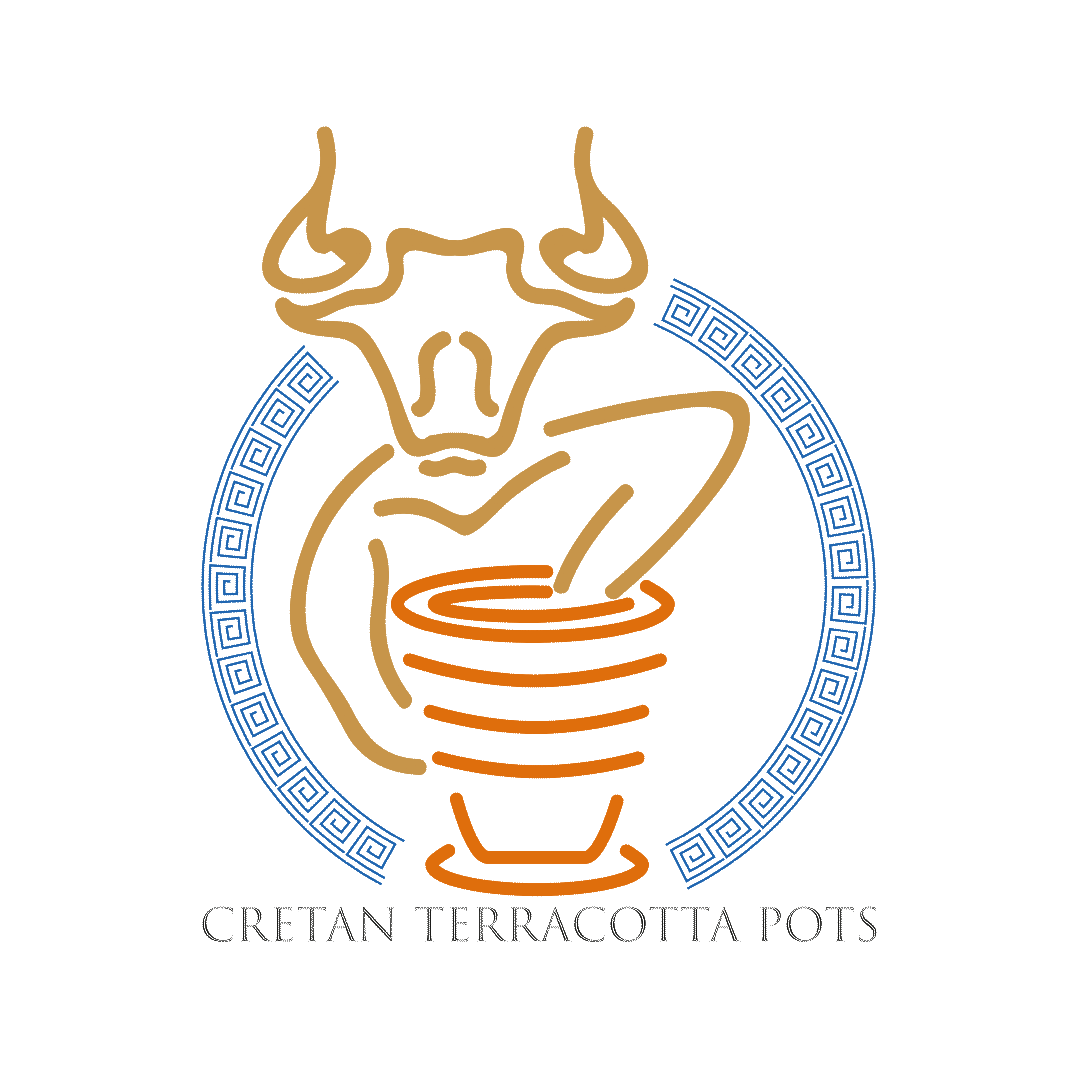
Following the traditions and processes evolved over many Millenia, today's Cretan potters, produce supremely high quality hand thrown terracotta, using only the local clay.

02
Celebrated for its inherent quality, the clay is first washed to remove impurities and mixed with water to achieve the right consistency for shaping.

03
The prepared clay is then formed into cylinders which the potter begins to shape on a potter’s wheel. Often, to achieve perfection, the wheel is still turned by hand as can be seen in our videos.

04
Many of the pots and jars are so large that they are made in distinct stages, with each preceding stage being allowed to dry over night before new clay is added and the next stage formed, sometimes over many days to achieve the larger pots.

05
All shaping of the pots is done by hand. There are no moulds used and only rudimentary tools to assist the process. It never ceases to amaze us, even now, how the potters sculpt many different shapes and sizes of pots, just through the skill of their hands, with no pattern to follow.

06
Looking into the potters’ workshops you would see many pots in all different stages of production.

07
Once the basic shape is finished, decoration is added. Rings, ropes, chains, handles and many other traditional devices, that bring the pot alive and give it that distinct Cretan quality. Again, all shaped by hand from clay slips.

08
The completed pots are taken outside to dry in the Mediterranean sun before being brought back into the workshop for firing. It is this stage that gives the pots their incredible robustness.

09
Pots are stacked on giant pallets before being slid into a gas fired kiln at 1200 degrees C. This is much hotter than kilns in other regions and enables the pots to withstand extremes of hot and cold without cracking.

10
Much is made of the advantages of traditional wood burning kilns, which do give the finished pot a mottled patina that some prefer. However, it is true that the gas kilns are more controllable, hotter, and give a more reliable firing and hence a better quality finished product.
The patina of both gas and wood fired pots changes very quickly outdoors as the porous nature of the terracotta creates its own local biome, giving the look that can be seen in our inspiration page and is the true joy of these very special pots.
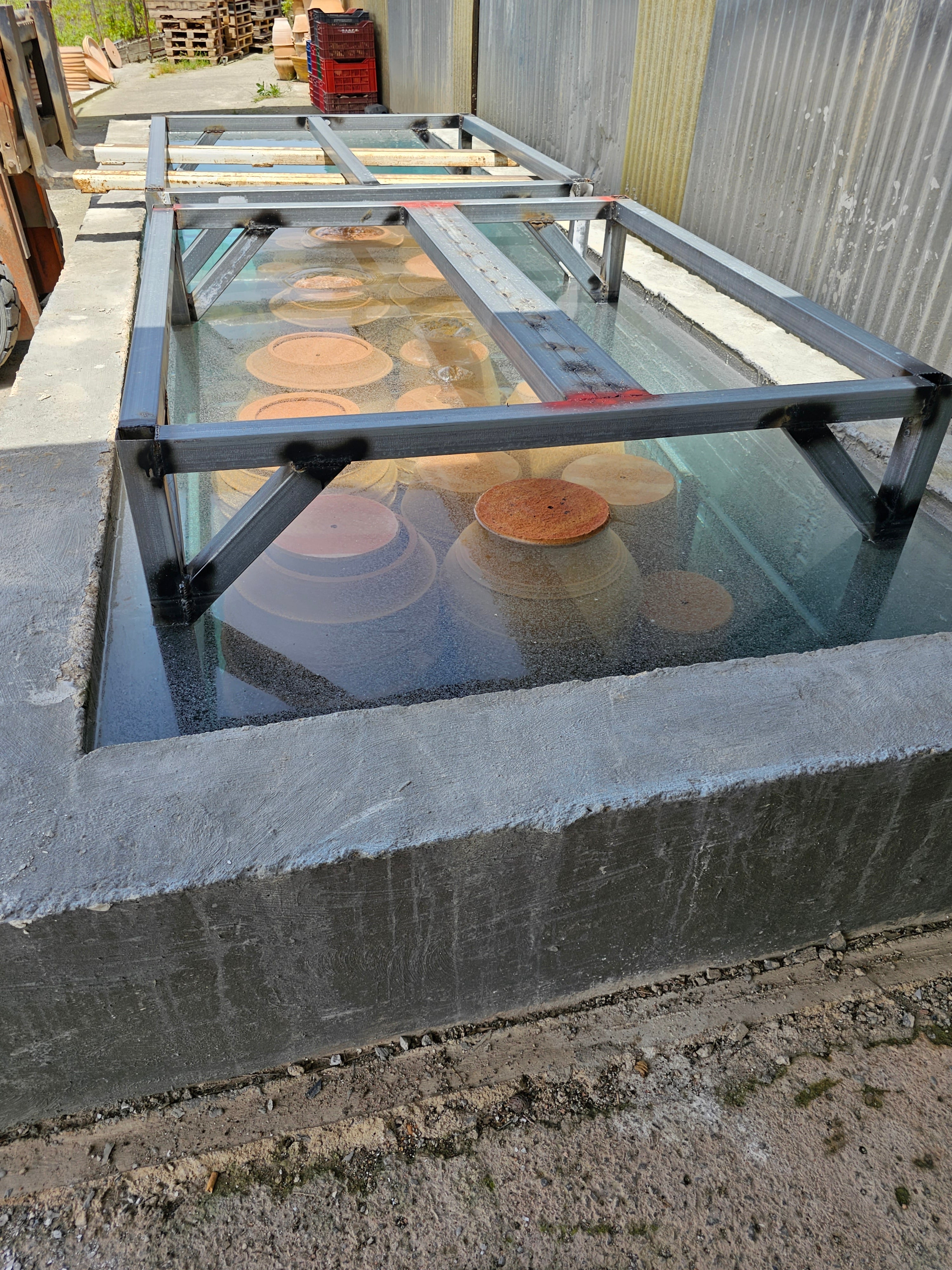
11Once the firing is complete and the pots start to cool they are
Once the firing is complete and the pots start to cool they are
plunged in our water baths for a day which gives them their final hardening in preparation for a long life bringing pleasure to all fortunate enough to own one.
01
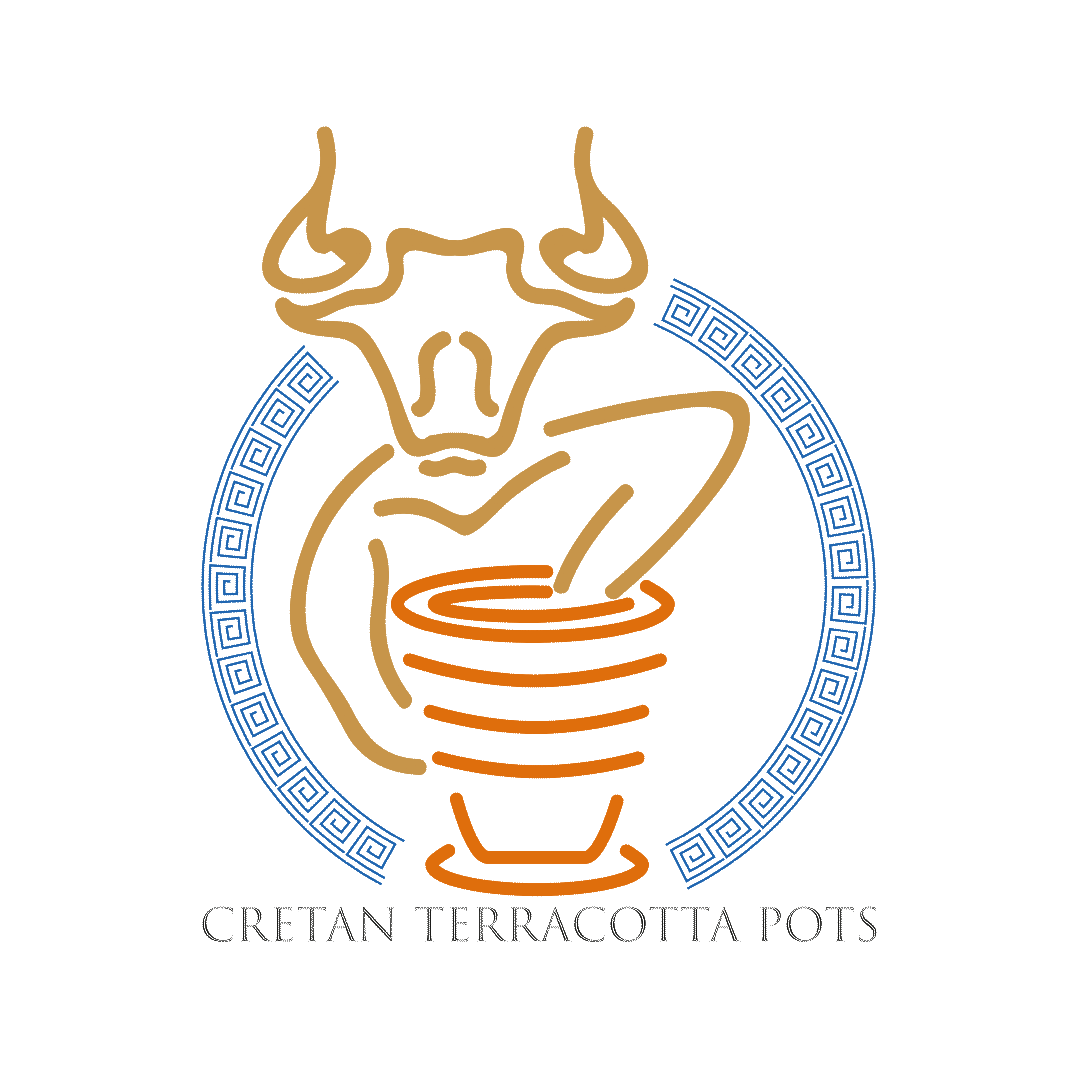
Following the traditions and processes evolved over many Millenia, today's Cretan potters, produce supremely high quality hand thrown terracotta, using only the local clay.
02
Celebrated for its inherent quality, the clay is first washed to remove impurities and mixed with water to achieve the right consistency for shaping.
03
The prepared clay is then formed into cylinders which the potter begins to shape on a potter’s wheel. Often, to achieve perfection, the wheel is still turned by hand as can be seen in our videos.
04
Many of the pots and jars are so large that they are made in distinct stages, with each preceding stage being allowed to dry over night before new clay is added and the next stage formed, sometimes over many days to achieve the larger pots.
05
All shaping of the pots is done by hand. There are no moulds used and only rudimentary tools to assist the process. It never ceases to amaze us, even now, how the potters sculpt many different shapes and sizes of pots, just through the skill of their hands, with no pattern to follow.
06
Looking into the potters’ workshops you would see many pots in all different stages of production.
07
Once the basic shape is finished, decoration is added. Rings, ropes, chains, handles and many other traditional devices, that bring the pot alive and give it that distinct Cretan quality. Again, all shaped by hand from clay slips.
08
The completed pots are taken outside to dry in the Mediterranean sun before being brought back into the workshop for firing. It is this stage that gives the pots their incredible robustness.
09
Pots are stacked on giant pallets before being slid into a gas fired kiln at 1200 degrees C. This is much hotter than kilns in other regions and enables the pots to withstand extremes of hot and cold without cracking.
10
Much is made of the advantages of traditional wood burning kilns, which do give the finished pot a mottled patina that some prefer. However, it is true that the gas kilns are more controllable, hotter, and give a more reliable firing and hence a better quality finished product.
The patina of both gas and wood fired pots changes very quickly outdoors as the porous nature of the terracotta creates its own local biome, giving the look that can be seen in our inspiration page and is the true joy of these very special pots.
11Once the firing is complete and the pots start to cool they are
Once the firing is complete and the pots start to cool they are
plunged in our water baths for a day which gives them their final hardening in preparation for a long life bringing pleasure to all fortunate enough to own one.










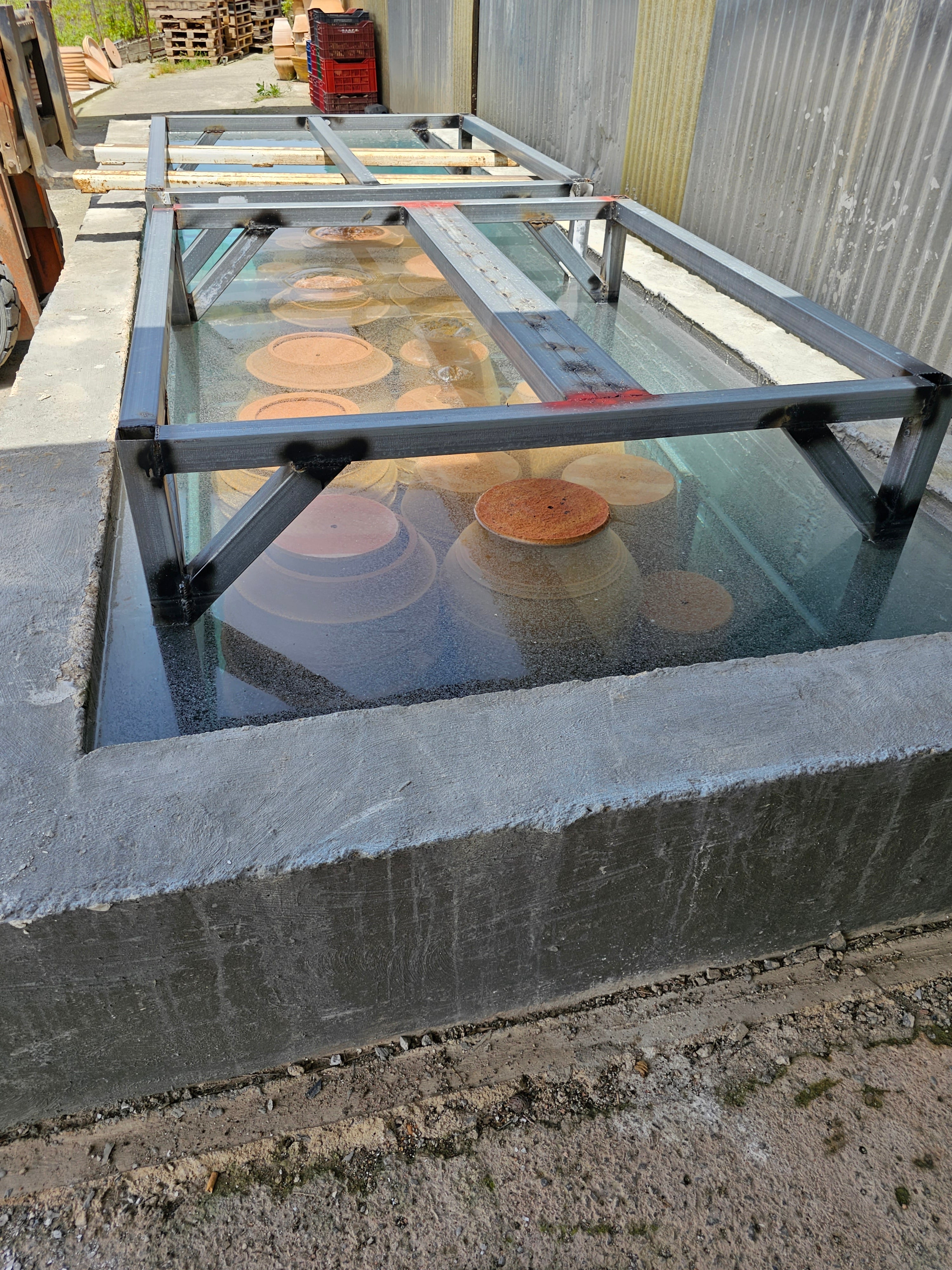
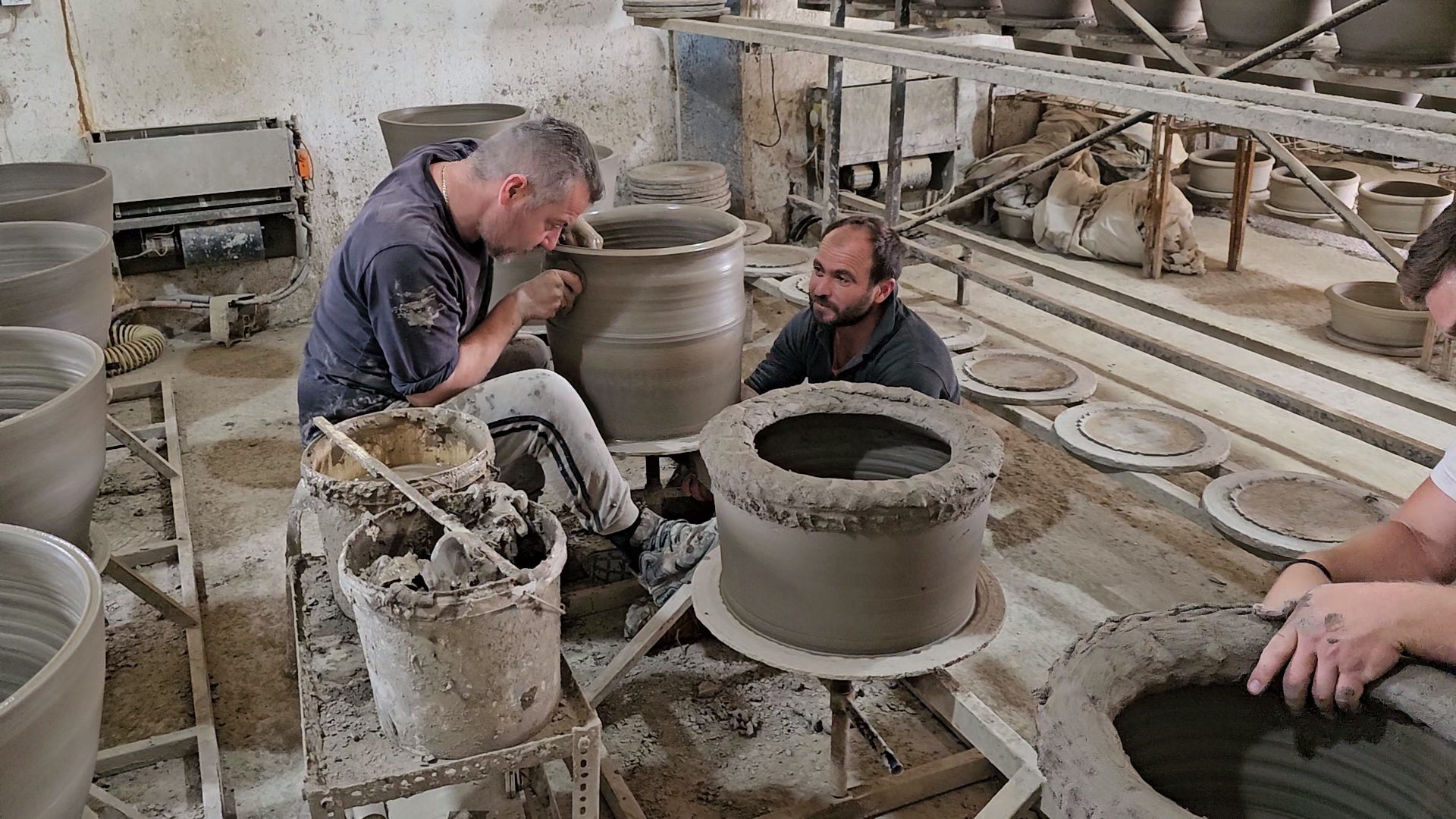
How Our Pots Are Made